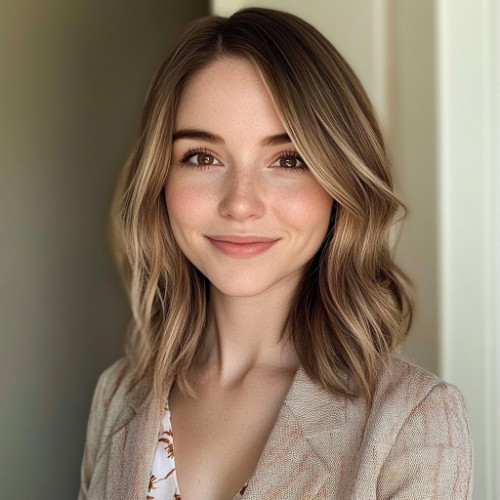
Emily Patterson
Senior Electronics Engineer
When we talk about additively manufactured electronics, or AME, we tend to think about conductive components — parts of the circuits ...
When we talk about additively manufactured electronics, or AME, we tend to think about conductive components — parts of the circuits themselves. But this is only part of the potential here.
With high-powered electronics, heat build-up is a real problem. This can put significant thermal stress on systems, resulting in failure. AME can provide the solution to this.
With AME, we can craft heat sink components that reduce this build-up. Due to the flexible nature of AME, we can craft components of specific shapes, drawing heat away from sensitive areas of the system and keeping devices functioning as they should.
Multi-material printing also adds other possibilities to the mix. We can develop highly effective thermal interface materials, based on metal, carbon, or polymer, to achieve optimal heat dissipation.
To put it simply, AME is crucial to the development of high-power electronics — every aspect of this development.