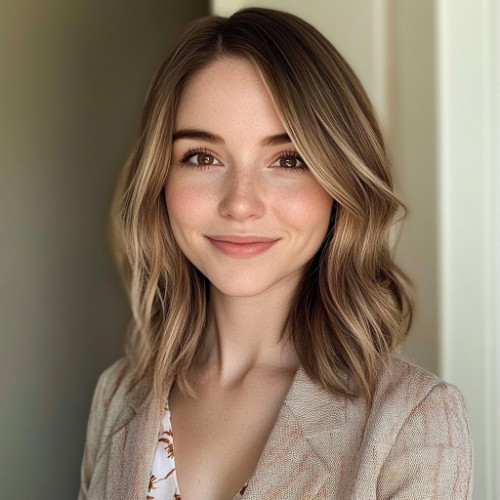
Emily Patterson
Senior Electronics Engineer
With fused deposition modelling (FDM), we take a filament, melt it, and then extrude it via a nozzle onto the printing bed. By building up ...
With fused deposition modelling (FDM), we take a filament, melt it, and then extrude it via a nozzle onto the printing bed. By building up different layers, we can develop components for electrical systems.
What are the benefits of this?
Firstly, it's cheap and easy, making customised components available to more users.
It's also compatible with lots of different materials, ideal if you're adopting a multi-material approach.
The potential for contamination is also low.There's little chance for external materials to work their way into your filament.
And what are the limitations?
It's not ideal for highly detailed printing, as we are limited by the size of the nozzle.
The method may also not be suitable for industrial components that will be under a lot of stress,as the cooling process happens at a different pace across each layer, leading to potential structural issues.
Despite the limitations,FDM is still a powerful option for developing larger components with multi-material printing.