How To Test, Validate, And Approve Materials For 3D Printing

A finished part is only as functional as the material it is constructed of. In high-stakes industries that demand extreme precision, like aerospace and advanced electronics, even minor discrepancies or inaccuracies in material properties can lead to catastrophic failures. This is why testing, validating, and approving materials for 3D printing is so critical to long-term success.
What Is Material Testing and Validation?
Validating 3D printing materials is the process of making sure they meet the mechanical, thermal, and chemical requirements of their intended application in the real world.
By testing materials prior to full-scale manufacturing, you can proceed with confidence in your product's integrity. In contrast, manufacturers that do not validate their materials risk compromised product performance, increased costs due to failed parts, and non-compliance with industry standards. All of these outcomes put your reputation and customer experience at risk.
Although testing and validation are integral to a successful outcome, they are not always easy. One major challenge is material variability. You might test batch 1 of a material and get favourable results. However, when you go into production with batch 2 of the same material, the print quality is subpar, and the performance is unacceptable.
Batch-to-batch consistency is not the only variable that can impact your results either. Environmental factors like temperature, humidity, and storage conditions also affect material performance. You want to address and account for these challenges to the best of your ability early in the development process. That way, you can trust your testing results.
How to Test Materials for 3D Printing
When planning your 3D printing material test, you might focus on the following properties:
- Thermal stability, which means materials withstand operating and printing temperatures without degrading
- Mechanical properties, which include tensile strength, elasticity, and impact resistance (this ensures longevity and performance under load)
- Dimensional accuracy, which tests for warping, shrinkage, and layer bonding
- Chemical resistance, which is critical to the materials that will be used in corrosive or chemically active environments
- Electrical conductivity, which ensures reliable signal transmission in circuits
The exact criteria you use will depend on the industry you operate in. Be sure to set relevant and application-specific goals when planning your tests. This will direct you towards the best 3D printing materials for your parts.
How to Validate 3D Printing Materials
There are several different ways you can approach validation. These include:
- Laboratory testing using ASTM and ISO standards
- Tests on the intended printer model to account for variations in hardware settings and build platforms
- Virtual simulations that replicate real-world conditions using software
- Environmental simulations, which test prototypes
- End-use performance testing to simulate operational stresses and validate material reliability
How to Approve 3D Printing Materials for Production
Approval processes ensure materials meet both technical and regulatory requirements. The steps involved include:
- Developing material specifications like performance benchmarks and acceptable variability
- Obtaining certifications like ISO 13485 for medical applications
- Performing supplier audits to ensure quality consistency and traceability
Plan, Prepare, Succeed
Testing and validating 3D printing materials is a multifaceted process. With the right approach and rigorous, application-specific testing criteria, you can proceed knowing your materials are capable of withstanding demanding applications.
Related Articles
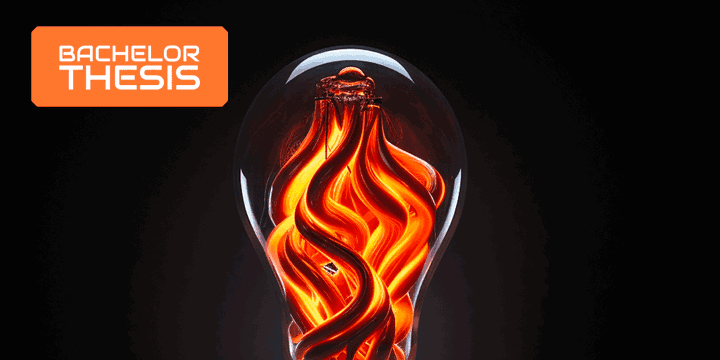
Signal Transmission Behavior Of Conductive Filaments In The Context Of Fused Filament Fabrication (FFF) Procedure

NScrypt - Supports NASA Mission To Revolutionize Space Exploration
